High-power Automatic Mirror Alignment System
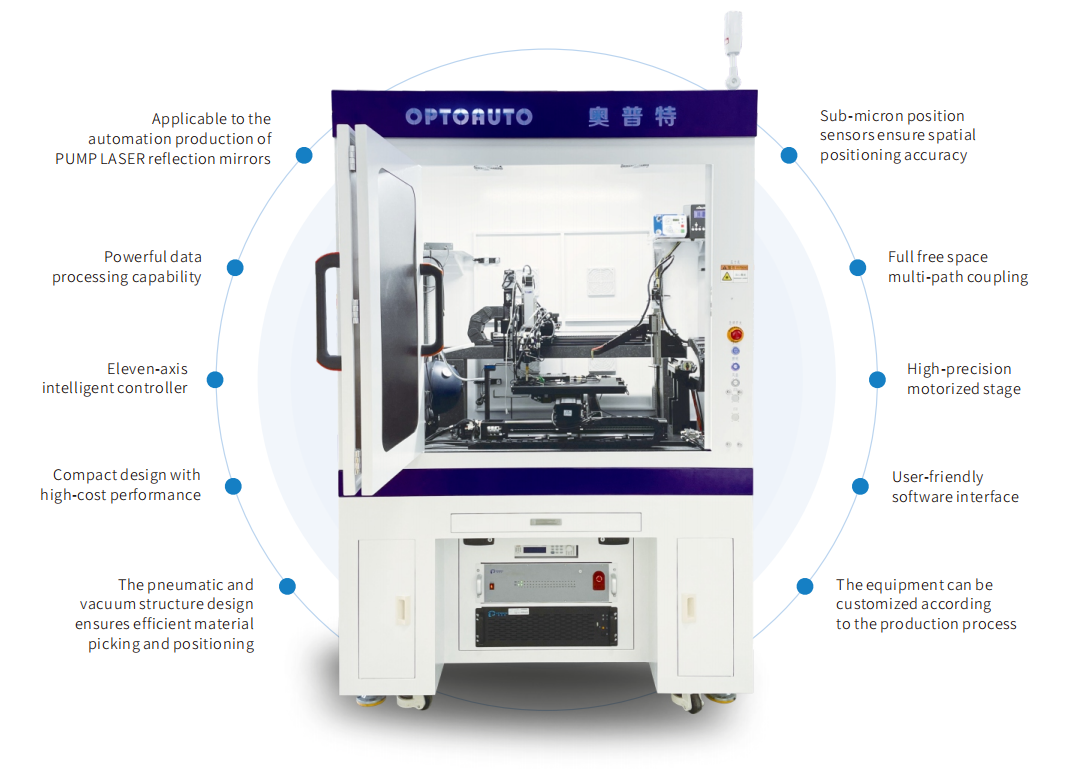
Our company’s independently developed High-power Automatic Mirror Alignment System (Model: OA11000-PLM) is designed for the fully automated production of array semiconductor fiber-coupled pump lasers. The system features a pneumatic and vacuum structure design to ensure efficient material picking and positioning, and uses high-precision stainless steel motorized stages to ensure precise movement in six-dimensional space. We provide an eleven-axis intelligent controller with self-developed operating software. Compared with manual assembly, this automatic alignment system can significantly improve production capacity, reduce dependence on skilled operators, and ensure product consistency.
The system comprises a coupling unit, automatic dispensing unit, imaging unit, control unit, and programmable control software. The core coupling unit features Japanese imported motors with high accuracy and long service life, ensuring long-term stable operation of the system. The combination of efficient algorithms, our unique control technology, and dispensing design ensures that the system’s comprehensive performance is comparable to that of imported equipment from abroad.
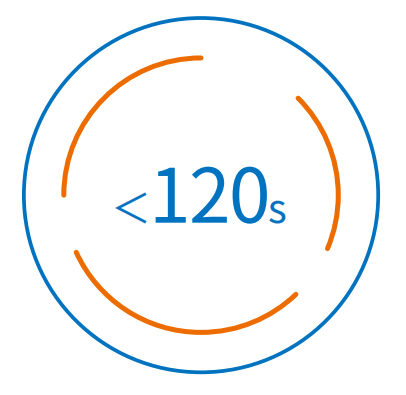
Single-channel coupling time (excluding curing)
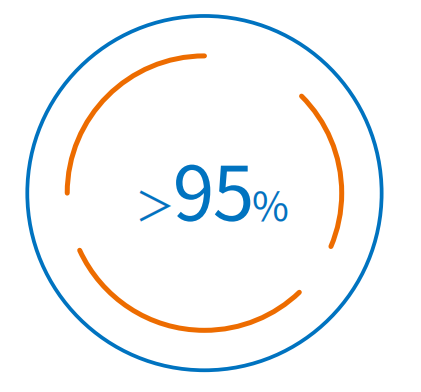
Coupling efficiency
Name | High-power Automatic Mirror Alignment System |
Model | OA11000 – PLM |
Pressure range | 0.6 ± 0.1 MPa |
Rated voltage | 220V / 16A |
Rated Power | 3 KW |
Power supply | (198~242) VAC,50Hz |
Vacuum source | -0.07Mpa |
Network | Cat5/6 |
Outline dimension | W1300xD1100xH2000mm (excluding the expanded portion of the observation window and the display) |
Weight | 800kg |
Operating environment | Avoid high temperatures and ensure good lighting in the working area. Do not expose the equipment to moisture and do not use it in workshops without adequate rain protection measures. For indoor use only. |
Equipment structural requirements | The equipment’s structural layout should be reasonable, with no interference between modules, and with sufficient clearance. |
Other requirements | ① The equipment’s design and manufacturing should feature advanced mechanical structure, process manufacturing, control systems, and user-friendly design, while ensuring safe operation. ② The necessary standard configuration for the equipment’s normal use must be complete and matching, including all corresponding accessories, cables, tools, and spare parts. |
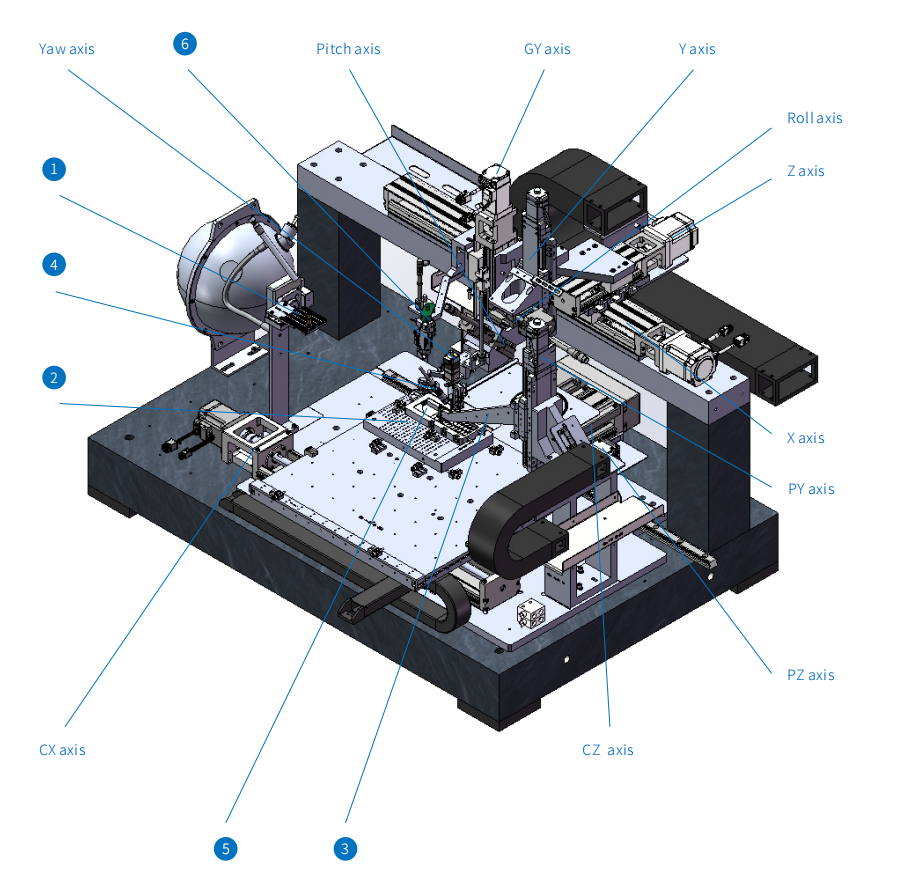
S/N | Name | Remarks |
1 | Automatic Feeder | Providing automated feeding and monitoring |
2 | Module positioning fixture | Mainly consisting of the platform positioning plate and custom-made modules |
3 | Automatic power-on device | Providing necessary travel for powering on |
4 | UV curing | To cure the glue with the UV rod |
5 | Reflective mirror picking fixture | Sucking the lens and ensuring suction accuracy with an attached sensor |
6 | Automatic dispensing device | For dispensing |
7 | X axis | Travel: 600mm, Unidirectional positioning accuracy: ≤25μm Repetitive positioning accuracy: ±3μm |
8 | Y axis | Travel: 100mm Resolution: {Full/Half: 4μm/2μm, Microstep(1/20 Microstepping) 0.2μm} |
9 | Z axis | Travel: 150mm, Unidirectional positioning accuracy: ≤20μm Repetitive positioning accuracy: ±3μm |
10 | CX axis | Travel: 540mm, Unidirectional positioning accuracy: ≤25μm Repetitive positioning accuracy: ±3μm |
11 | CZ axis | Travel: 540mm, Unidirectional positioning accuracy: ≤25μm Repetitive positioning accuracy: ±3μm |
12 | GY axis | Travel: 200mm, Unidirectional positioning accuracy: ≤20μm Repetitive positioning accuracy: ±3μm |
13 | PY axis | Travel: 100mm Resolution: {Full/Half: 4μm/2μm,Microstep(1/20 Microstepping) 0.2μm} |
14 | PZ axis | Travel: 100mm Resolution: {Full/Half: 4μm/2μm,Microstep(1/20 Microstepping) 0.2μm} |
15 | θX (Pitch axis) | Travel: ±4°, Repeated positioning accuracy: within ±0.001° |
16 | θY (Yaw axis) | Travel: 270°, Positioning accuracy: 0.0144° |
17 | θZ (Roll axis) | Travel: ±4°, Repeated positioning accuracy: within ±0.001° |
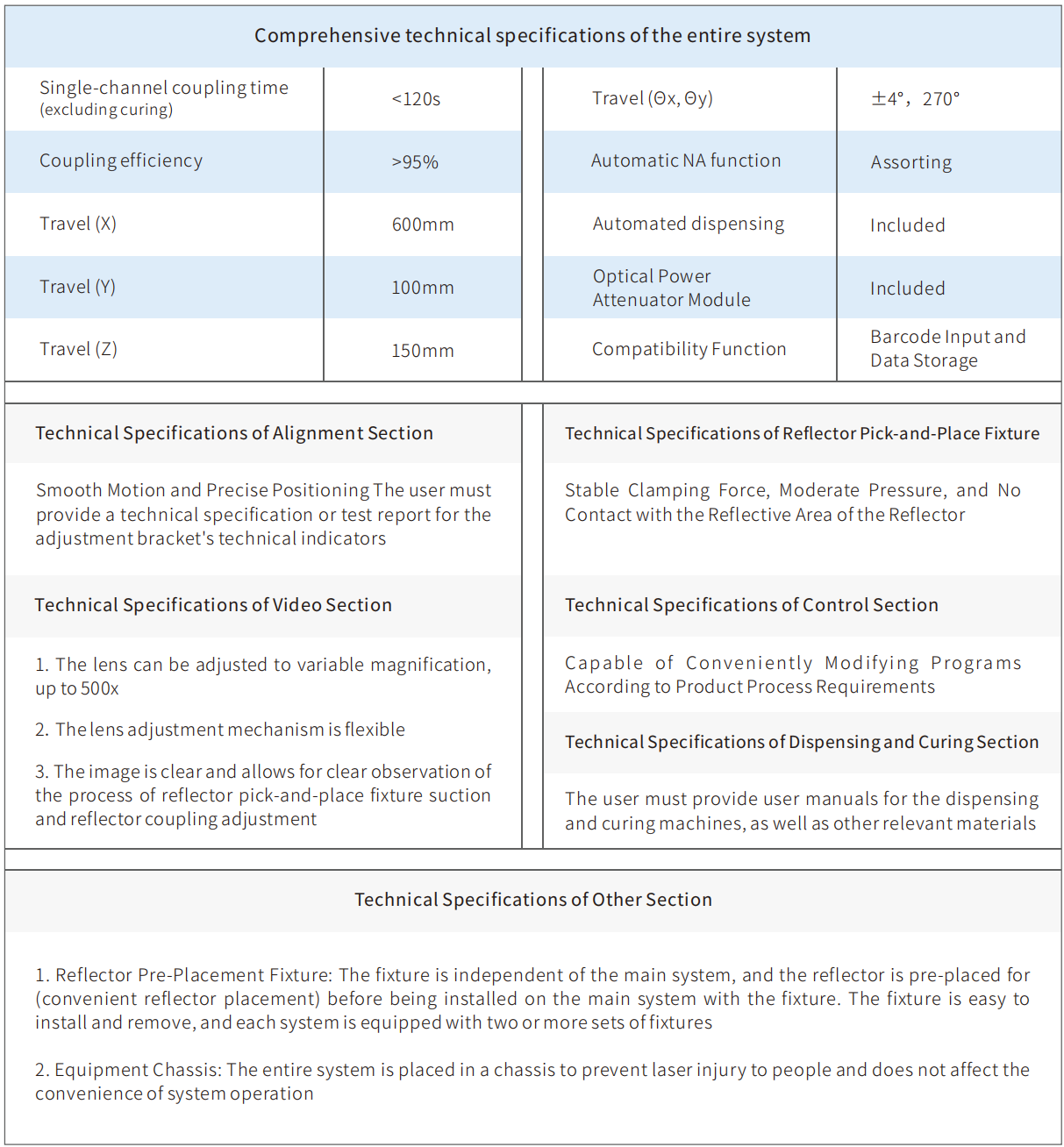